Ospiti di STADLER Anlagenbau GmbH e di Iren Spa, abbiamo visitato l'impianto di selezione e stoccaggio della plastica "Circular Plastic" a Borgaro Torinese (TO). Il sito, al momento il più grande d'Italia, tratta circa 100.000 tonnellate di plastica e lattine miste all'anno riuscendo ad inviare fino all'80% dei rifiuti in ingresso agli impianti di riciclaggio
A poco più di 14 km da Torino, più precisamente a Borgaro Torinese, sorge Circular Plastic il nuovo e moderno impianto di selezione e stoccaggio della plastica nato dalla collaborazione tra STADLER, azienda tedesca leader nella progettazione, produzione e assemblaggio di impianti di riciclaggio e selezione chiavi in mano e Iren Spa, la principale multiutility del nord Ovest.
Una collaborazione, quella tra l'azienda tedesca e la multiutility italiana, iniziata nel 2020 e consolidatasi in numerosi progetti di successo come: l'impianto RAEE di Iren a Volpiano (TO), l'impianto di riciclo della plastica di Pianezza (TO), l'impianto ReCap a Parma che tratta sia plastica che cartone e l'impianto Valterza ad Asti che seleziona rifiuti di plastica mista costituiti principalmente da bottiglie e film.
Per questo motivo, forte dei traguardi raggiunti insieme, anche per la progettazione e l'installazione di Circular Plastic, Iren ha scelto il know-how di Stadler.
Un impianto da record a Nord di Torino
L'impianto di Borgaro Torinese con i suoi 77mila mq di superficie è al momento il sito più grande d'Italia e tratta circa 100.000 tonnellate all'anno di plastica proveniente dai circuiti di raccolta differenziata effettuata dai cittadini. Il sito tratta sia i rifiuti sfusi, derivati dalla raccolta della plastica mono/multimateriale del comprensorio torinese, sia la plastica già preselezionata e pressata in altri impianti dell'Italia centro-settentrionale. In particolare ha, come proprio principale conferitore, l'impianto di preselezione di Pianezza (TO) che tratta il materiale della città di Torino. All'interno degli impianti di preselezione vengono estratte le impurità presenti, non valorizzabili, o altri materiali come l'alluminio, il ferro e le cassette dell'ortofrutta.
Una volta che i rifiuti arrivano all'interno dell'impianto avviene una prima fase di prelavorazione del materiale in ingresso e il caricamento, mediante l'utilizzo di un escavatore con benna a polipo, della macchina lacera-sacchi che convoglia il materiale avviato a lavorazione verso un vaglio rotante STADLER, un cilindro della lunghezza di 12 mt e del diametro di 3 mt, dotato di fori a dimensione crescente.
Il materiale sfruttando la pendenza, la rotazione e la crescente dimensione dei fori del vaglio viene separato in 3 flussi: ingombrante, medio e fine. Il materiale ingombrante viene vagliato con un modello speciale di separatore balistico STADLER STT5000, che garantisce una migliore separazione dei film, e poi separato in cabina di selezione. Vediamo invece il percorso del materiale fine e medio all'interno dell'impianto.
La linea dedicata al materiale fine
La linea dedicata al materiale fine è uno dei fiori all'occhiello di Circular Plastic. Su questa linea i materiali di piccola pezzatura vengono trattati mediante un separatore magnetico e un separatore a correnti indotte in modo da riuscire ad estrarre dal flusso tutto il materiale ferroso e l'alluminio, quindi vengono separati tramite un vaglio rotante STADLER e due separatori ottici per recuperare piccoli componenti plastici come tappi di bottiglia e altri materiali valorizzabili.
La linea del materiale medio
Il materiale di dimensioni medio viene diviso su due linee tramite una tramoggia con tamburo di separazione dove in entrambe ritroviamo il separatore balistico STADLER STT5000, per separare rispettivamente i materiali 2D (flessibile) e 3D (rigido), mentre i materiali di piccola pezzatura tornano alla linea dedicata al materiale fine.
I lettori ottici con scanner a infrarossi consentono di separare le plastiche per polimero e colore.
Il materiale 2D viene lavorato tramite una linea dedicata composta da 6 separatori ottici che permettono di separare diverse tipologie di film (PP, PE e bio-film). Il flusso 3D, invece, una volta liberato dai materiali ferrosi tramite separatore magnetico, viene trattato in una linea dedicata con separatori ottici che separano: PET chiaro, PET blu, PET colorato, PET opaco e le vaschette.
Ulteriori separazioni ottiche garantiscono un aggiuntivo controllo di qualità automatico e la pulizia di questi prodotti principali. Parallelamente, su una linea dedicata, vengono separate le frazioni di HDPE, PS e PP. Dal materiale residuo delle due linee 3D viene ulteriormente separato l'alluminio.
All'interno dell'impianto è inoltre presente una linea dedicata al ricircolo dei materiali valorizzabili. Tutti i materiali residui dalle separazioni delle linee 2D e 3D sono sottoposti ad ulteriore separazione ottica in modo da identificare e separare i materiali valorizzabili ancora presenti che vengono quindi reintrodotti nella linea di separazione del materiale 3D. Questa linea, oltre ai separatori ottici, include un sistema fora bottiglie, un separatore balistico STT2000 STADLER e un sistema di dosaggio per garantire il miglior ricircolo del materiale.
Una volta terminato il processo di selezione ottica e dimensionale, la plastica viene stivata in box di accumulo contenenti ciascuno un prodotto diverso. Il ciclo termina con la pressatura del materiale, attraverso due linee che creano balle monomateriale pronte per essere stoccate in magazzino e gestite dai consorzi autorizzati. L'impianto è dotato di un avanzato sistema di celle di carico per monitorare la quantità del materiale in ingresso e le quantità dei diversi materiali stoccati nei bunker pronti per l'imballaggio. Questo sistema permette all'operatore, incaricato della gestione delle presse imballatrici, di conoscere in ogni momento la quantità esatta di materiale presente nei bunker in modo da organizzare le operazioni di pressatura al meglio per produrre un numero preciso di balle di ogni prodotto.
Grazie alle soluzioni innovative e alle tecnologie avanzate presenti l'impianto è in grado di selezionare automaticamente 17 tipi di polimeri e plastiche, alluminio e materiali ferrosi, garantendo la massima flessibilità operativa. Questo processo produce un output di alta qualità, restituendo fino all'80% dei materiali in ingresso al ciclo di riciclaggio.
Dietro le quinte: sfide progettuali e tecnologia all'avanguardia
Progettare un impianto di questa portata, imponente sotto diversi punti di vista (mq totali, numero di macchine presenti, capacità di trattamento, quantità di materiali trattabili etc) ha presentato durante le varie fasi di sviluppo numerose sfide che il team STADLER è riuscito a fronteggiare grazie alla vasta esperienza del Costruttore tedesco. "Durante la fase di progettazione, abbiamo dovuto studiare come ottimizzare lo spazio per collocare tutte le macchine nell'edificio, garantendo le manutenzioni e i futuri ampliamenti. Inoltre, durante la fase di assemblaggio, la sfida è stata coordinare più di 100 maestranze per comporre l'impianto e tutti i sistemi ausiliari. Infine, una volta completato il montaggio, dovevamo garantire che l'impianto potesse lavorare l'elevato flusso di materiale, pari a 20 tonnellate all'ora, senza sbocchi del materiale o fermi dell'impianto, garantendo sempre l'elevato livello di quantità e purezza di tutti i prodotti in uscita", ha dichiarato Paolo Cravedi, Senior Project Manager di STADLER. Parole di apprezzamento per il lavoro svolto da STADLER sono state espresse anche da parte di Iren. "In ogni fase, abbiamo apprezzato la capacità di STADLER di adattare il layout e il design alle nostre esigenze, sfruttando la loro grande esperienza nell'ingegneria degli impianti per scegliere le migliori soluzioni tecniche", ha spiegato l'Ing. Flaviano Fracaro, Direttore Tecnico di Iren Ambiente.
La tecnologia STADLER al servizio dell'uomo
All'interno dell'impianto la tecnologia STADLER è stata utilizzata sia per facilitare le normali operazioni di esercizio delle macchine sia per garantire la migliore accessibilità per le operazioni di manutenzione.
Un nuovo pannello mobile, collegabile in ogni area dell'impianto, permette agli operatori di gestire localmente gli avviamenti delle singole macchine, facilitando le operazioni di manutenzione grazie a speciali sensori di rilevamento, installati sui motori, è inoltre possibile ottenere dati utili per la manutenzione preventiva delle macchine. Tutti i dati e i segnali raccolti sono disponibili e possono essere gestiti da remoto tramite un software dedicato che monitora e registra più di 1000 segnali contemporaneamente per generare report periodici sull'andamento dell'impianto e sulle operazioni di manutenzione.
Infine la cabina di selezione è dotata di un efficiente sistema di climatizzazione che mantiene un ambiente di lavoro confortevole durante tutto l'anno, garantendo 10 ricambi d'aria all'ora con aria fresca dall'esterno. "Ciò che apprezziamo di più dell'impianto è la gestione dello spazio nel layout, con passaggi che rendono tutte le macchine accessibili e l'intero impianto facile da percorrere, garantendo un eccellente accesso per la manutenzione. Inoltre, grazie ai vari sistemi di gestione per gli operatori, è molto facile e intuitivo controllare e gestire l'intera struttura", ha confermato Fracaro.
Circular Plastic mantiene la promessa insita nel nome; mentre Iren grazie alla tecnologia e al supporto offerto da STADLER riesce davvero a rendere il percorso della plastica circolare: da scarto a nuova risorsa.
Altri contenuti simili
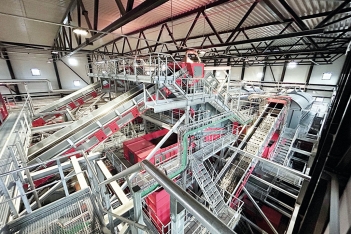
La rivoluzione dei rifiuti urbani a Stoccolma
Il nuovo impianto per la selezione dei rifiuti urbani “Resursutvinning Stockholm”, progettato e costruito da STADLER Anlagenbau GmbH per la...
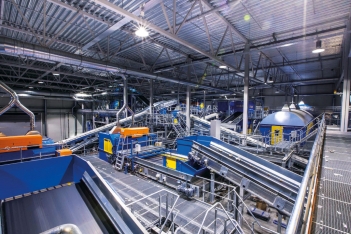
Riciclo ed economia circolare: Paesi scandinavi verso nuovi traguardi
STADLER Anlagenbau GmbH, realtà di riferimento a livello internazionale nelle soluzioni chiavi in mano per impianti di riciclo e selezione,...
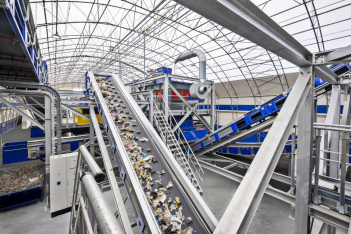
Il punto di vista di STADLER sul riciclo della carta
La domanda di imballaggi sostenibili sta crescendo rapidamente, con un focus sull’industria alimentare, che da tempo preferisce imballaggi cartacei. STADLER,...
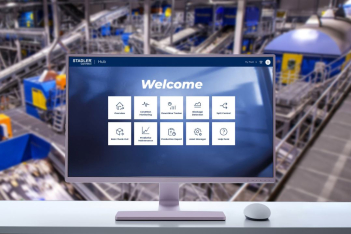
Soluzioni digitali STADLER: una nuova era per il riciclo con impianti “intelligenti” e performanti
STADLER Anlagenbau GmbH, azienda tedesca specializzata nella progettazione, produzione e assemblaggio di impianti di riciclaggio e selezione chiavi in mano,...
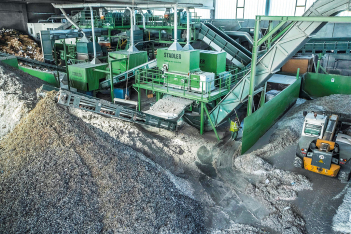
Riciclare per decarbonizzare
Combustibile derivato da rifiuti per l’industria del cemento: la sfida della selezione Il Combustibile Derivato da Rifiuti (CDR), prodotto dai Rifiuti...
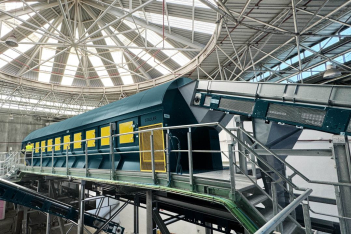
Inaugurato in Spagna il nuovo impianto di selezione realizzato da STADLER
La nuova struttura sostituisce un impianto preesistente, incrementando la capacità da 3 a 8 tonnellate all’ora, migliorando l’efficienza e garantendo...
.jpg)
STADLER WireX rivoluziona la rimozione automatica del filo dalle balle
STADLER Anlagenbau GmbH presenta alla fiera IFAT di Monaco di Baviera WireX, la nuova macchina per la rimozione automatica del filo...
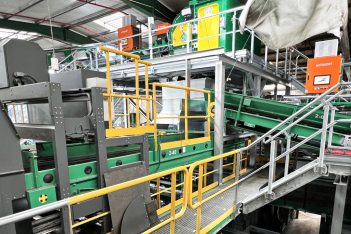
STADLER progetta e installa un impianto di riciclo per imballaggi leggeri in Portogallo
STADLER Selecciona S.L.U. (una consociata di STADLER Anlagenbau GmbH) ha progettato e installato un impianto di riciclo degli imballaggi plastici...
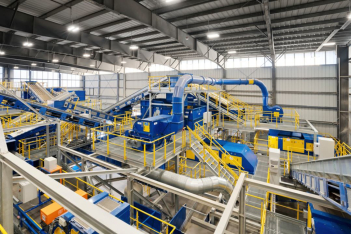
STADLER e Krones chiudono il ciclo della plastica nel Polymer Center di Las Vegas
STADLER Anlagenbau GmbH, in collaborazione con Krones, ha progettato e installato il nuovo Republic Services Polymer Center di Las Vegas,...
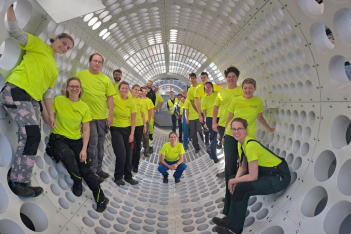
La collaborazione lungo la catena del valore è la chiave per un’economia circolare
STADLER Anlagenbau GmbH, l’azienda tedesca attiva a livello globale e specializzata nella progettazione, produzione e assemblaggio di impianti di riciclo...